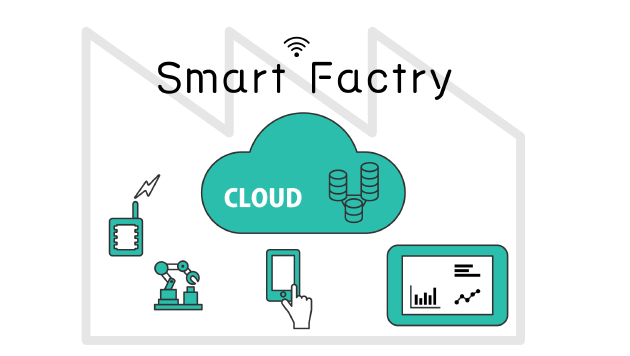
近年、工場内設備や装置のIoT化が注目されております。
*本投稿は、こちらからもダウンロードできます。
長期的かつ大容量な稼働状況データが活用できるようになるため、長期的な生産管理や複数のデータ分析による複雑な異常検知が可能となります。
IoTシステムを工場に導入するためには主に二つの課題があります。一つは工場設備へのセンサ取付や各種情報をどのように取得しサーバへ吸い上げるかです。もう一つはサーバに吸い上げたデータをどのように活用するかです。
ここでは、汎用製品や既存インフラを利用し、いかに短期間、安価かつ安全にIoTシステムを導入するかについて、具体的な方法をご紹介します。
さらに、 PLC 経由で取得したデータをサーバ環境まで伝送・連携するためにはネットワークや IT 関連の技術が必要となります。
上記課題に対応するために、各種PLC プロトコルを標準搭載したFA 仕様の PLC ゲートウェイを利用することができます。ここでは、スタンドアローンや小型設備などの小規模向け小型ゲートウェイ「 PUSHLOG 」( GUGEN 社)と、充実したネットワーク接続と高い耐久性により大規模運用まで対応可能な IoT コントローラ「 FC6A Plus 」( IDEC 社)について説明します。
導入のメリットと課題
生産現場にIoTを導入することで、設備の稼働状況が把握できるようになり、生産性向上や保守の効率化が期待できます。長期的かつ大容量な稼働状況データが活用できるようになるため、長期的な生産管理や複数のデータ分析による複雑な異常検知が可能となります。
IoTシステムを工場に導入するためには主に二つの課題があります。一つは工場設備へのセンサ取付や各種情報をどのように取得しサーバへ吸い上げるかです。もう一つはサーバに吸い上げたデータをどのように活用するかです。
ここでは、汎用製品や既存インフラを利用し、いかに短期間、安価かつ安全にIoTシステムを導入するかについて、具体的な方法をご紹介します。
PLC ゲートウェイの活用
工場にIoT を導入するためには、生産設備や装置の制御に伴ってさまざまなデータを送受信する PLC との連携が必要となります。しかしながら PLC に用いられるプログラミング言語やプロトコルは機種ごとに異なるため、対象の PLC に熟知した人材が必要となります。さらに、 PLC 経由で取得したデータをサーバ環境まで伝送・連携するためにはネットワークや IT 関連の技術が必要となります。
上記課題に対応するために、各種PLC プロトコルを標準搭載したFA 仕様の PLC ゲートウェイを利用することができます。ここでは、スタンドアローンや小型設備などの小規模向け小型ゲートウェイ「 PUSHLOG 」( GUGEN 社)と、充実したネットワーク接続と高い耐久性により大規模運用まで対応可能な IoT コントローラ「 FC6A Plus 」( IDEC 社)について説明します。
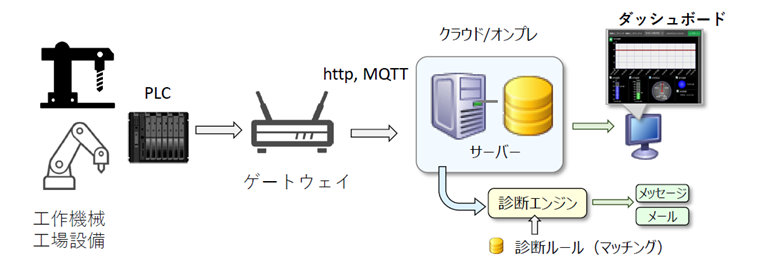
図1 PLC ゲートウェイを活用した IoT システムの構成例
小型PLCゲートウェイの活用
まずはじめに、各種PLCプロトコルを標準搭載したFA仕様の小型ゲートウェイ「PUSHLOG」(GUGEN社製)があります。PUSHLOGは各種プロトコルを標準搭載、PLCとプログラムレスで簡単に接続することができます。
・三菱電機、キーエンス、オムロン社などのPLCと接続が可能
・携帯回線網を活用してセンサーデータをクラウドに転送
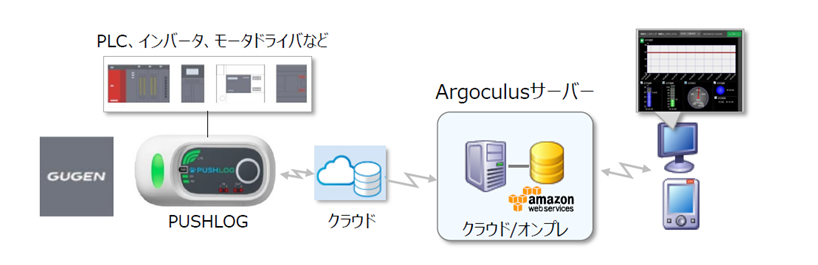
図2 PUSHULOGを活用したIoTシステム構成例
サイエンスソリューションズ社製IoTプラットフォームArgoculusと連携することで、収集されたデータの蓄積、可視化、制御、データ処理、異常診断、セキュリティなど様々なIoTの機能が利用可能となります。
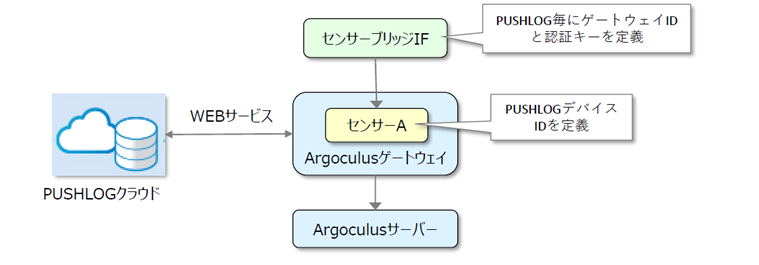
図3 ArgoculusサーバーとPUSHULOGクラウドとの連携
IoTコントローラの活用
次に、各種情報ネットワーク接続機能を備えたIDEC社製IoTコントローラ「FC6A Plus」について説明します。FC6A Plusは様々な拡張モジュールに対応しており、デジタル入力、アナログ入力による0-10V、4-20mA、測温抵抗体の取り込みが可能。また、一般的な通信プロトコルであるModbus、EtherNet/IP、MCプロトコルに対応しており、様々なデバイスと通信することも可能です。
情報ネットワーク接続機能としては、FTPサーバー、FTPクライアント機能によって、ログデータファイルの転送が可能です。さらに、MQTTプロトコル対応によりArgoculusサーバーへのデータ転送を効率的に実現することができます。
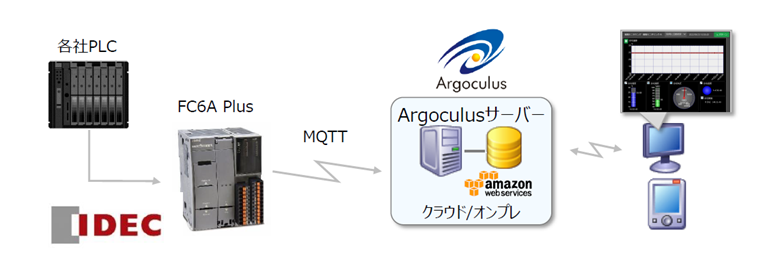
図4 FC6A PlusとArgoculusサーバーとの接続例
オールインワン IoT プラットフォーム
工場にIoT システムを導入することにより、これまで単独で使われていた機器や装置を遠隔から監視・運用することが可能になります。拠点間にまたがる設備の稼働データや生産状況などのデータを共有し、有効活用することにより効率的な運用や保守管理が可能となります。IoTプラットフォーム Argoculus を利用することにより、 IoT システムに必要な様々な機能を簡単かつ安全にサーバー上に構築することができます。各種センサーデータのモニタリング、ビッグデータの蓄積、利用、分析支援が可能となり、真のデータ活用を実現いたします。
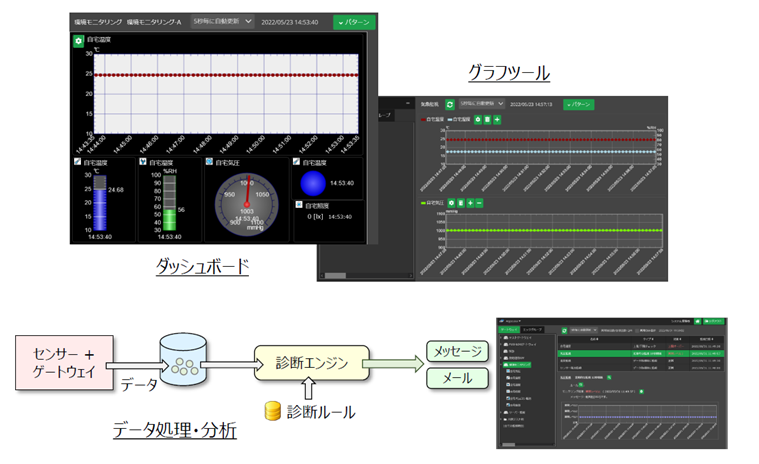
図5 Argoculus の IoT 機能例
高圧水ポンプの異常検知システム
高圧ポンプに設置した電流・振動センサからIoT ボックス(ゲートウェイ)経由でクラウドサーバーにデータを収集します。サーバー上でArgoculus を利用することにより、データ活用に必要な機能とルールベース診断機能を兼ね備えた異常検知システムを構築いたしました。
ポンプの状態とポンプ破損の要因であるフィルタの詰まりを自動監視・分析し、システム取り付け前に多発していたポンプ破損の回避に成功しました。
同一システム上でデータ収集、可視化、異常検知、データ分析、通知機能が利用できるため、システム開発の時間を大幅に削減し、短期間での導入・運用が可能となりました。
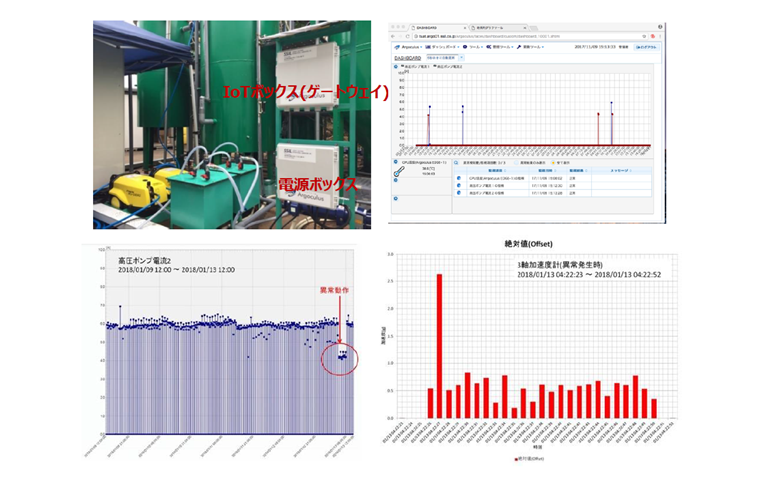
図6 高圧水ポンプの異常検知システム